Something I haven't talked about is annealing the aluminum before you try to form it, so here goes.
-use a dirty acetylene only flame to put a layer of soot on the surface
-change the oxy-acet flame to a neutral flame and heat the entire piece until you make the soot disappear and reveal nice clean alum
-let the alum air cool, and it's annealed
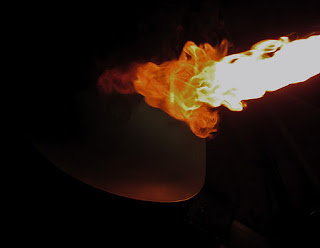
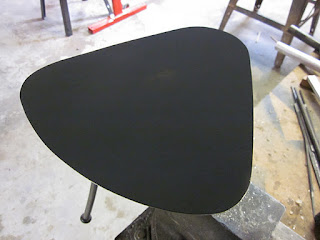
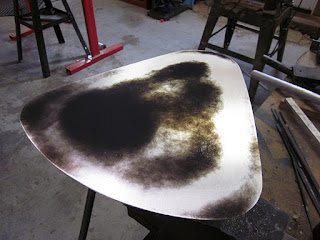
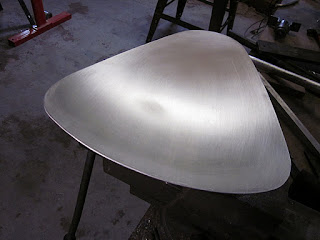
I decided to hammer the back panel of the oilbag, so it's back to the buck.
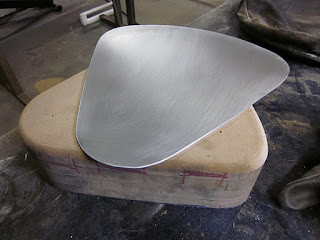
Fitted

Welded
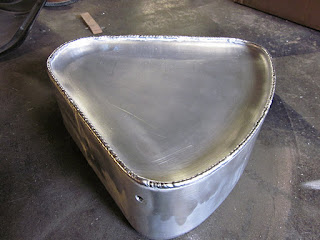
Top mounts